Exactly How to Avoid Weld Undercut: Vital Tips for Welders
Exactly How to Avoid Weld Undercut: Vital Tips for Welders
Blog Article
Understanding the Art of Welding: How to Stay Clear Of Undercut Welding Issues for Flawless Fabrication Outcomes
Effectiveness and accuracy are critical on the planet of welding, where even the least imperfection can jeopardize the architectural stability of a produced item. One usual challenge that welders face is undercutting, an issue that can damage a weld joint and lead to costly rework. By comprehending the source of undercut welding and executing reliable techniques to avoid it, welders can boost their craft to brand-new levels of quality (Preventing weld undercut). In the search of flawless fabrication results, understanding the art of welding to prevent undercut issues is not just a skill however a need for those aiming for perfection in their work.
Understanding Undercut Welding
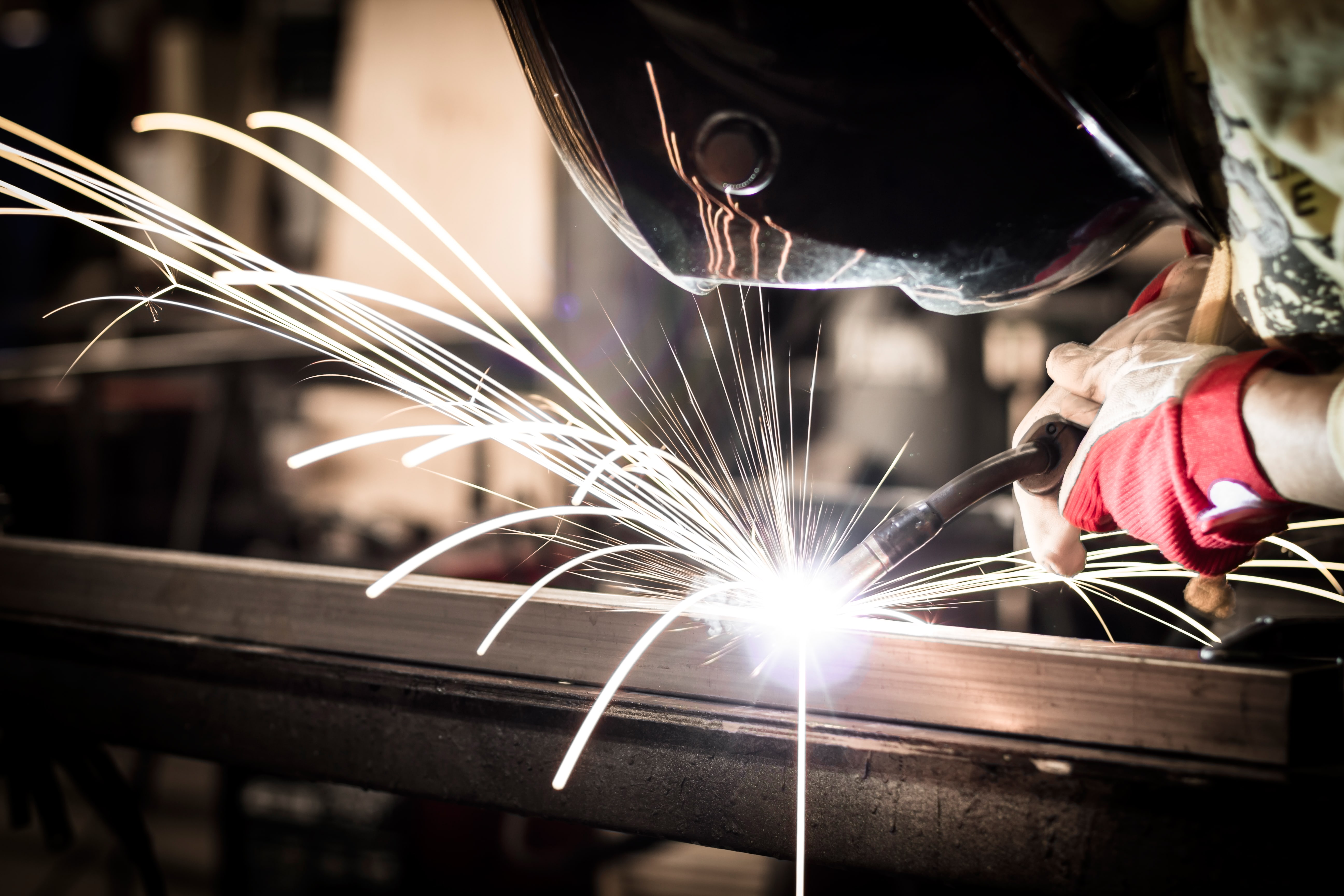
To avoid undercut welding, welders need to make sure proper welding specifications, such as adjusting the present, voltage, travel rate, and maintaining the right electrode angle. In addition, utilizing the appropriate welding strategy for the particular joint arrangement is important. Using weaving movements or backstepping strategies can help make sure appropriate weld steel deposition and reduce the possibility of undercut development. Normal evaluation of welds throughout and after the welding procedure is additionally essential to capture any kind of undercut very early and make necessary modifications to stop further defects. Preventing weld undercut. By recognizing the sources of undercut welding and implementing safety nets, welders can attain high-quality, structurally sound welds.
Reasons For Undercut in Welding
Recognizing the elements that add to damage in welding is vital for welders to produce top notch, structurally audio welds. Insufficient welding inaccurate or existing welding speed can additionally contribute to undercut. Recognizing these causes and executing correct welding techniques can assist protect against undercutting problems, making certain strong and long lasting welds.
Methods to stop Undercutting

To alleviate the danger of undercutting in welding, welders can use critical welding strategies intended at improving the high quality and stability of the weld joints. Furthermore, utilizing the appropriate welding technique for the specific joint configuration, such as weave or stringer grains, can add to minimizing damaging.
Additionally, proper joint preparation, consisting of making certain tidy base products without contaminants and using the appropriate welding consumables, is critical in protecting against undercut flaws. Utilizing back-step welding methods and controlling the weld grain profile can also aid disperse heat equally and lessen the danger of undercut. Regular examination of the weld joint during and after welding, as well as applying high quality assurance actions, can help in attending to and spotting damaging problems without delay. By carrying out these techniques carefully, welders can achieve remarkable fabrication results with marginal undercut problems.
Relevance of Proper Welding Specifications
Picking and maintaining suitable welding criteria is essential for accomplishing effective welds with marginal defects. Welding specifications describe variables such as voltage, existing, take a trip rate, electrode angle, and shielding gas flow price that directly impact the welding process. These specifications have to be carefully changed based on the kind of product being bonded, its density, and the welding strategy used.
Correct welding parameters ensure the correct amount of warm is applied to melt the base metals and filler material consistently. If the specifications are set too expensive, it can cause too much heat input, triggering distortion, burn-through, or spatter. On the other hand, if the parameters are also reduced, incomplete fusion, absence of infiltration, or undercutting may occur.
Quality Control in Welding Operations
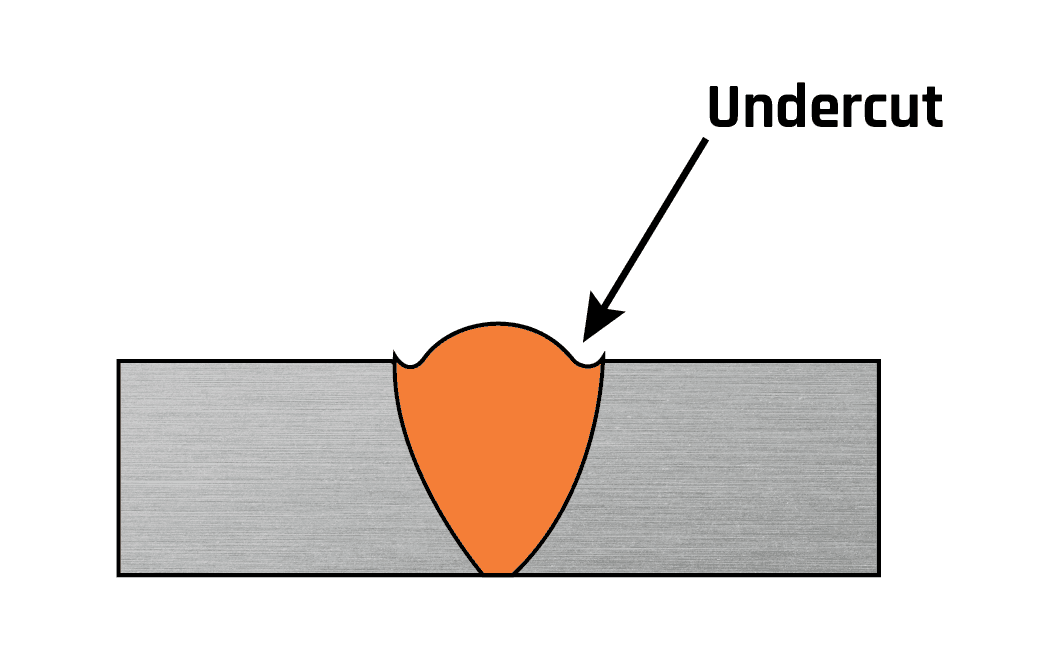
Verdict
In verdict, grasping the art of welding needs an extensive understanding of undercut welding, its causes, and strategies to avoid it. By making sure proper welding criteria and carrying out high quality assurance techniques, flawless manufacture outcomes can be achieved. It is crucial for welders to constantly pursue excellence in their welding procedures to avoid undercut concerns and create high-quality welds.
Undercut welding, an usual problem in welding procedures, happens when the weld steel doesn't properly fill up the groove and leaves a groove or depression along the bonded joint.To prevent undercut welding, welders must ensure correct welding parameters, such as changing the current, voltage, travel rate, and maintaining the appropriate electrode angle. Poor welding incorrect or existing welding speed can likewise add to undercut.To alleviate the threat of undercutting in welding, welders can utilize critical welding techniques intended at boosting the quality and stability of the weld joints.In verdict, mastering the art of welding needs a detailed understanding of undercut welding, its causes, and methods to avoid it.
Report this page